MASUMA PRODUCTION
Masuma spare parts are manufactured both at our own factories and at the facilities of our partners in Asia-Pacific region. There are more than 40 modern factories, producing OEM parts for Japanese and American vehicle manufacturers among other products.
Masuma's primary manufacturing facility is based in the south of China in Guangzhou, where undercarriage parts are manufactured. The company’s plants are ISO-9001 certified and equipped with Japanese equipment and staffed with qualified personnel.
All products are manufactured at the request and under control of the parent company Masuma Auto Spare Parts Japan, which owns all the technologies used in the production process.
BRAKE PADS PRODUCTION
Masuma manufactures more than 600 types of disc and drum brake pads for Asian and European brands. General properties of Masuma pads are identical to those of the original OEM parts.
The quality of the friction material of the pads plays a key role. During more than 10 years we developed and tested various formulations, achieving thermal stability of the compound, low noise levels and minimal formation of dust and chips. The friction material consists of two dozen components that affect the properties of the pads. For example, metal shavings (usually brass or bronze) provide efficient heat dissipation, and bonding elements provide high mechanical strength.
Each finished batch of pads undergoes several stages of testing for compliance with ECE R-90, SAE J866, SAE J661 and Masuma's own standards:
- Basic test. It simulates braking at a speed of 100 km/h to check the friction coefficient of unheated pads.
- Hot test. During dynamic driving, brake pads’ temperature can be as high as 300 ° C and more. Operation of the pads is necessarily checked at high temperatures in a lab environment/
- Cyclic test. One of the toughest braking modes is driving on a mountain road. During the cyclic test, similar conditions are created: acceleration up to 100 km/h and braking down to 50 km/h, again acceleration and again braking - up to 50 or more cycles. Thus we can evaluate the performance of the friction material under extreme conditions.
- Recovery test. During this test the characteristics of the brake pads are assessed after cooling down following critical heating.
- Burst test. The quality of the connection of friction lining with the metal base (plate) must be checked during the tensile test.
BRAKE DISC PRODUCTION
Masuma brake disc plant is equipped with high-tech equipment: lines for vertical and horizontal forming, casting cooling, machining and others. Most of the machines are made in Japan. Extensive automation minimizes the likelihood of rejects. High-strength nodular cast iron (VChShG) is used for production of brake discs. High precision of castings with tolerances down to a few microns guarantees the correct geometry of the disc and absence of runout and vibrations during operation. Almost all Masuma brake discs feature a non-directional coating on the running surface. This ensures that the pads are lapped quickly and evenly after installation. Each finished batch of discs undergoes several stages of testing for compliance with TUV, ABE, KF2-GVO 1400/2000, TS16949, ISO 9001: 2000 standards and Masuma's own standards:
- Chemical analysis. Allows to evaluate the quality of the alloy of the discs, strength and other characteristics.
- Spectral analysis. Shows accuracy of maintaining the alloy formulation during casting.
- Test for abrasion resistance. In lab environment abrasion resistance of discs is evaluated at different usage patterns at different temperatures.
- Hardness measurement. Disc material is checked for compliance to specified hardness values according to the HRB classification (Rockwell hardness).
Discs are treated with an oil-free anti-corrosion compound, which guarantees the safety of products even in warehouses with high humidity. The oil-free compound does not affect the performance of the brake pads, so it does not need to be removed before mounting discs on a vehicle.
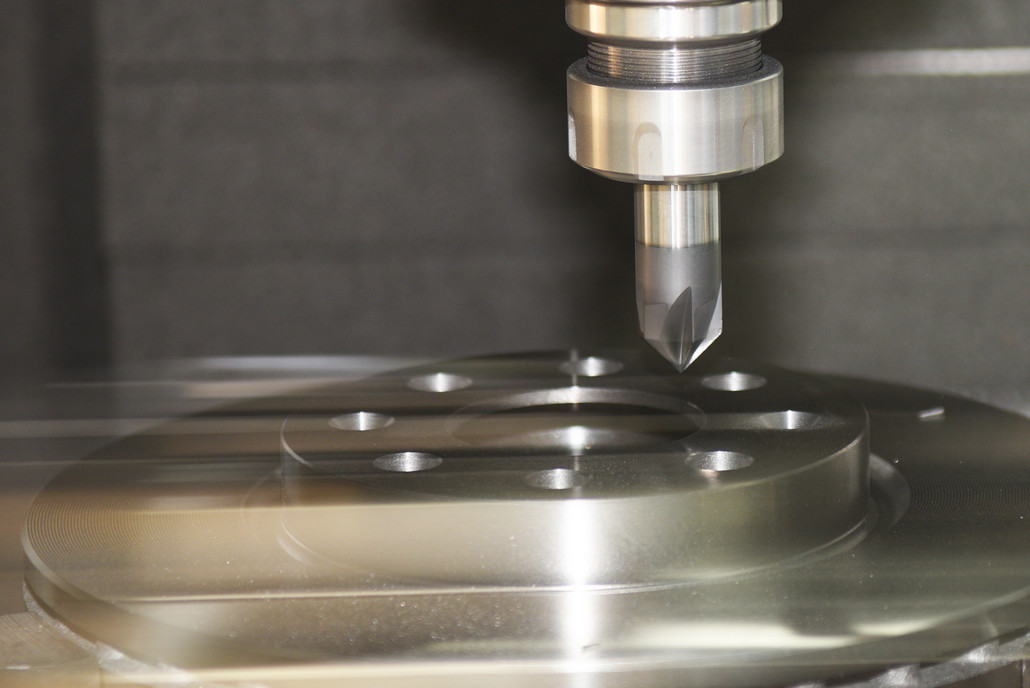
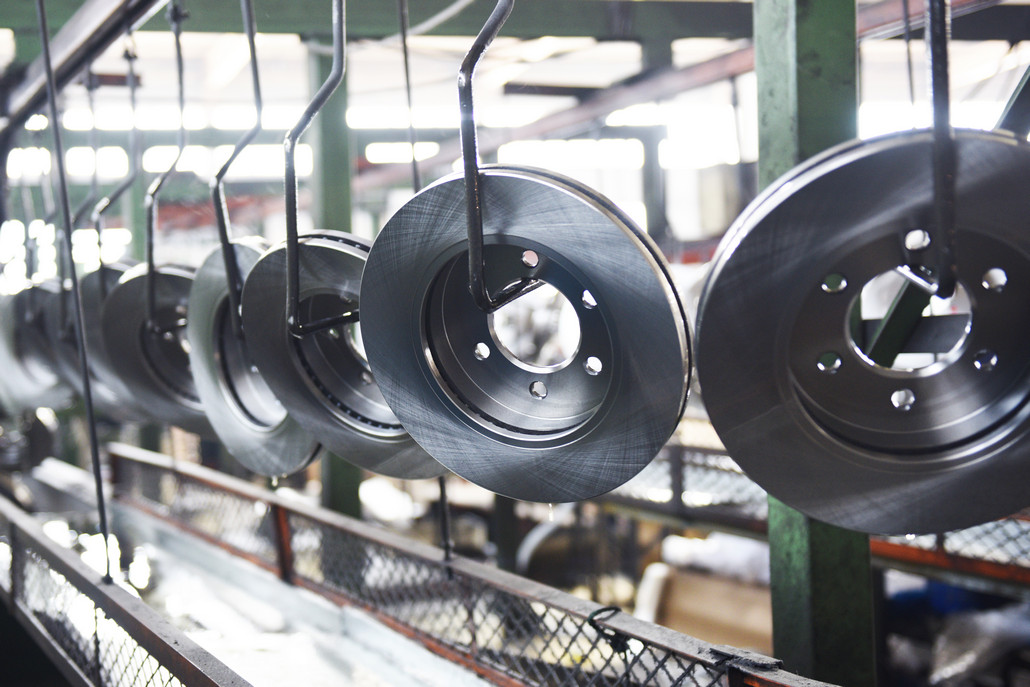
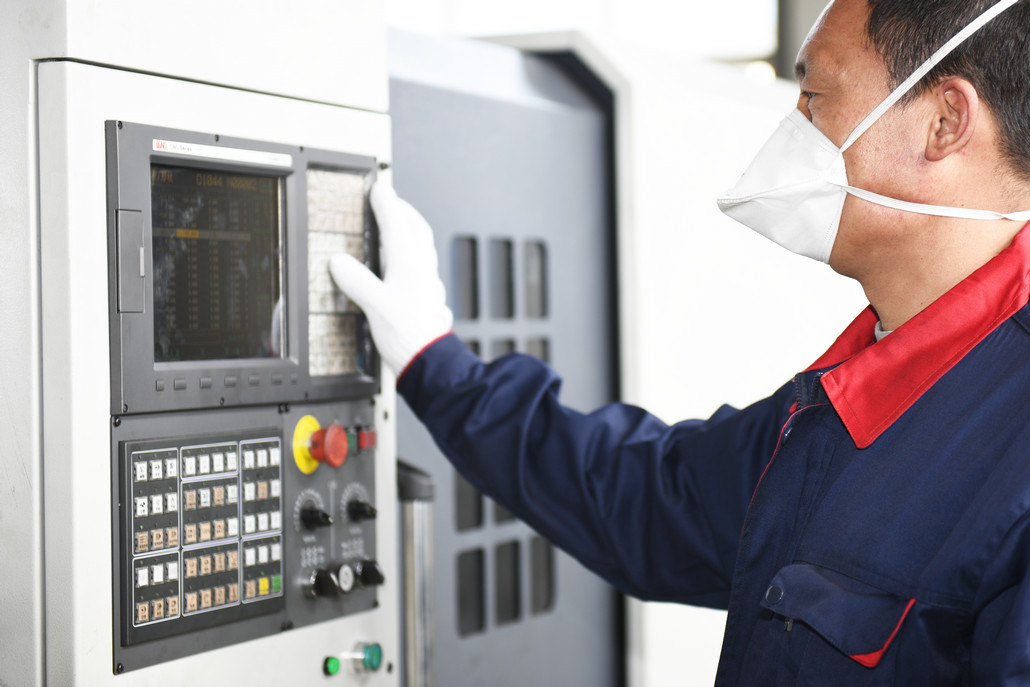
FUEL PUMP PRODUCTION
Masuma gasoline pumps are manufactured at ACDelco plant, a well-known American manufacturer of spare parts with more than 100 years’ experience, owned by General Motors. The plant produces parts both under its own brand and for third-party customers. The quality of the products is the same.
The production lines of the plant are equipped with high-precision Japanese equipment that requires minimum manual operations. Operators just control the machines and perform control measurements.
The plant has a multi-level quality control system. First, key indicators of a fuel pump are checked for compliance with the set values:
- maximum pressure;
- actuation of the bypass valve;
- productivity;
- power demand;
- internal resistance.
This is followed by resource tests in the laboratory. With the help of heat chambers, vibration stands and other installations, they simulate real operational conditions and external environment impact, checking the part’s reliability. Only after that the batch is sent for packaging.
WIPER PRODUCTION
Thanks to technical partnership with car manufacturers Masuma wipers are fully equivalent to specifications of OEM wipers.
Wiper blades are produced of a mixture of natural rubber and synthetic polymer, which provides optimum resistance to abrasion and temperature changes. The estimated lifespan of a wiper is not less than a million strokes.
Graphite in the rubber compound ensures that a wiper glides effortlessly on glass. Graphite concentration is carefully controlled during production process. If it is not enough, friction will be too heavy, which will lead to cloudy glass. An excess of graphite leads to lower quality of cleaning. Therefore, the composition of the rubber compound is checked twice: at the production stage and during final testing a wiper.
Wipers from each batch are checked according to a special checklist:
- composition of the rubber mixture;
- strength and elasticity of the material;
- temperature resistance and other types of resistance;
- quality of wiper’s adherence to the surface;
- cleaning efficiency on a real windshield.
A steel strip is situated in any wiper (even frameless), which ensures a tight and even adherence of a wiper to the windshield. Durable steel with carefully developed features is used for its production which:
- retains elasticity during the entire service life;
- protects against corrosion and aggressive washing fluids;
- has a precisely matched shape for a specific car model.
During production of wiper frames attention is paid not only to strength but also to aesthetic appearance throughout all the wiper’s service life. Thus there are 3 layers of finish: special primer, with which the parts are coated by full immersion, and two layers of powder paint.
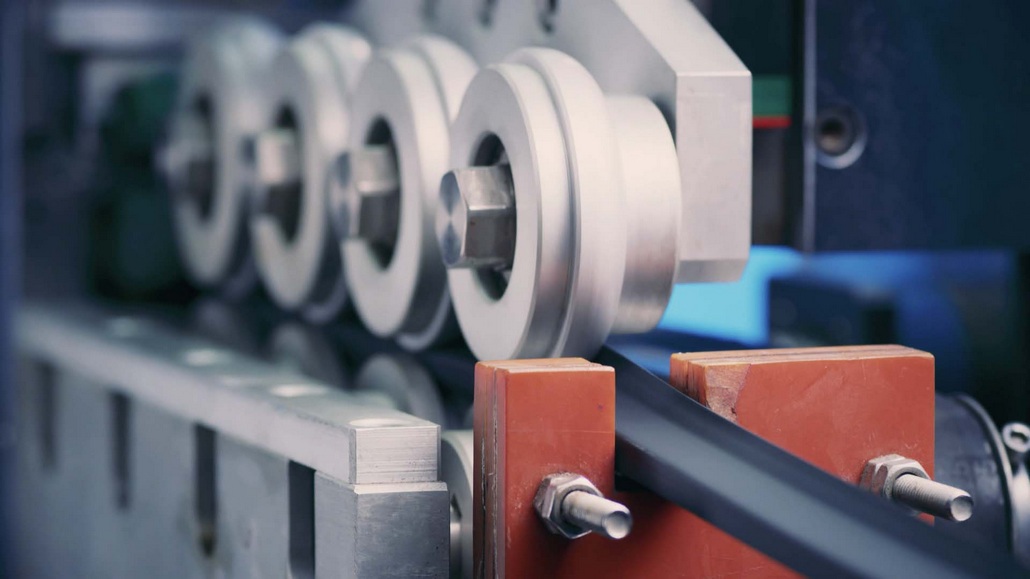
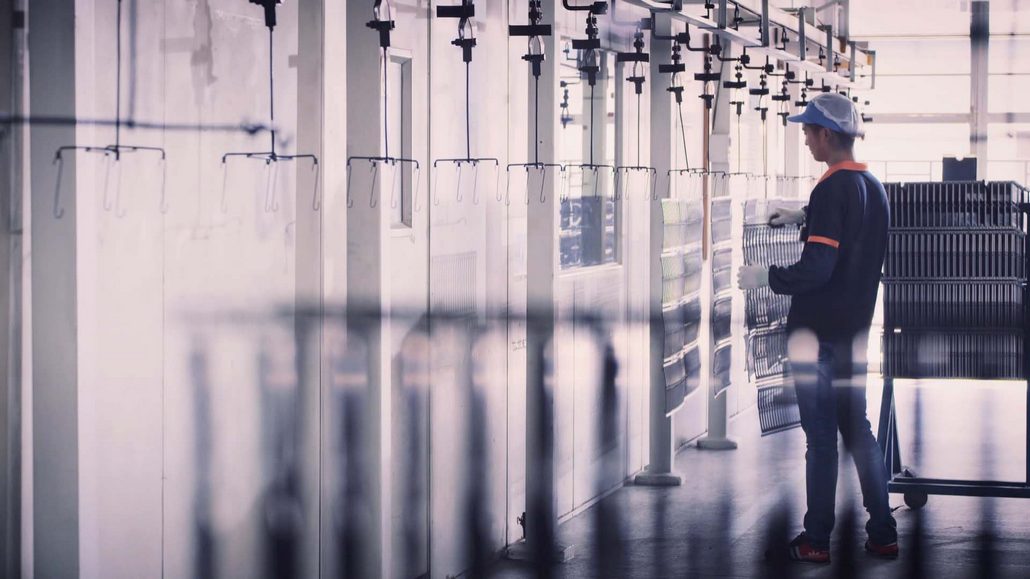
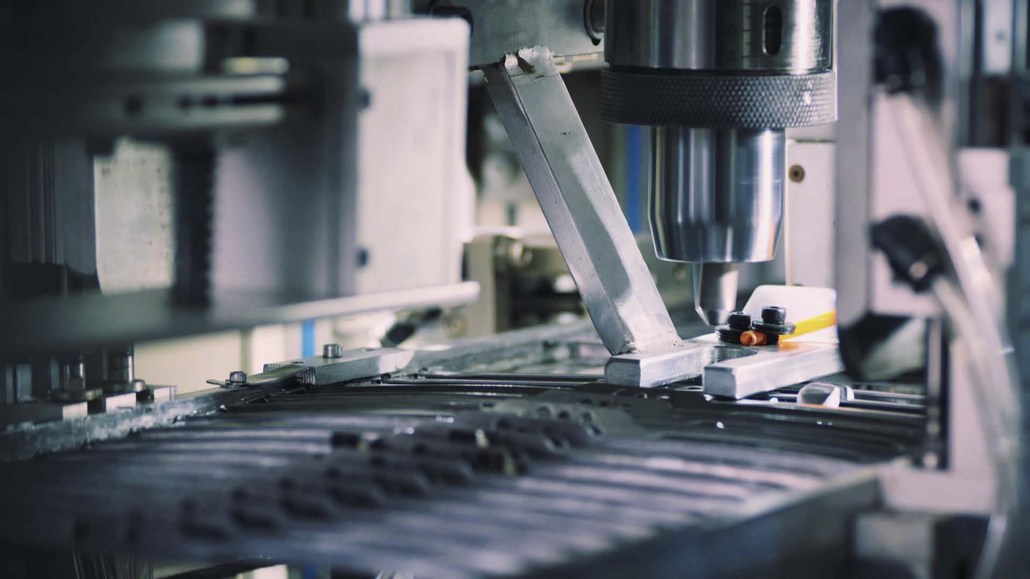
SILENT BLOCK PRODUCTION
Silent blocks are rubber-metal hinges that connect almost all the major components of a vehicle suspension. These components not only ensure the mobility of different bars and rods, but also to absorb shocks from road surface. Therefore Masuma does not use polyurethane and other hard polymers, but produces rubber-based silent blocks, as vehicle design suggests.
We managed to find the optimal rubber compound - strong and elastic at the same time, which provides good damping with an impressive service life. Reliable vulcanization of rubber when connected to metal eliminates displacement of a silent block from its inner cage.
Japanese equipment is used during production: CNC lathes, vacuum furnaces for rubber preparation, etc. The automation is nearly full: wherever manual operations can be abandoned, we have done it. This approach minimizes the risk of errors.
The plant has its own testing laboratory, where silent blocks are tested according to dozens of indicators:
- crash tests for rubber separation from metal components of silent blocks;
- tests for torsion, compression, tension and other types of deformation;
- assessment of the impact on the silent block because of vibration of various frequencies, shocks and other load types;
- checking the operation of products at different temperatures and humidity levels.
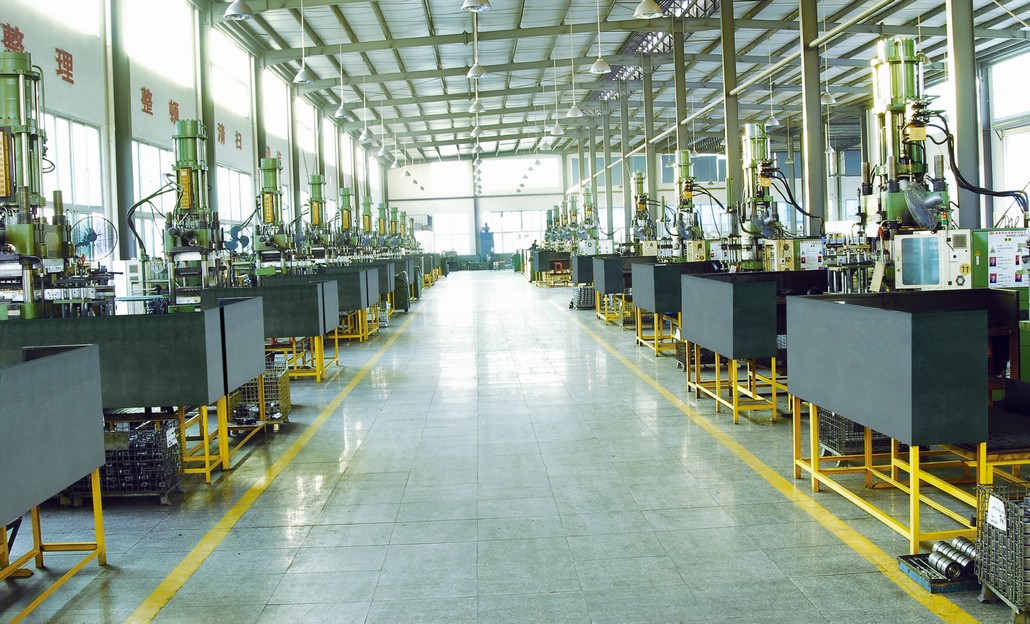
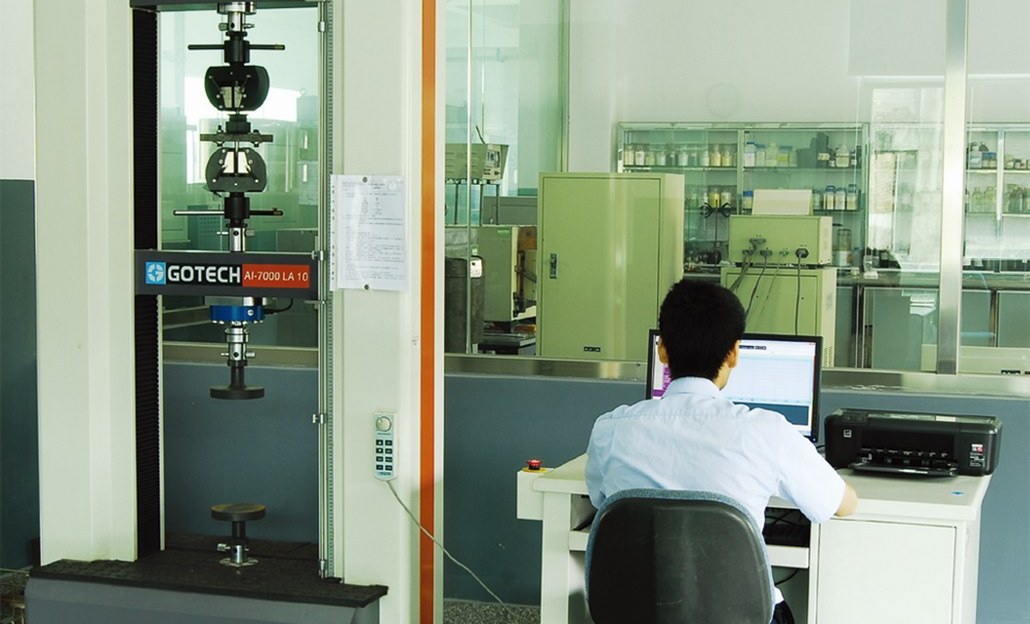
SUSPENSION ARM PRODUCTION
Masuma's suspension arms are designed with specific vehicle models in mind, focusing on the best combination of strength and lightness. Masuma bars are made of Mn65 carbon tool steel and Cr40 and Cr20 alloy structural steel - the same as in the original Japanese machine levers. The plant also produces parts from light alloys.
The arms are welded by automatic machines. Geometric dimensions and weight distribution of parts are also controlled by automation, which guarantees high manufacturing accuracy.
Depending on the design, bars can be equipped with rubber-metal hinges (silent blocks) and ball bearings, or supplied without them.
Features of Masuma bars:
- Impact-resistant anticorrosive coating protects metal from road reagents and rust;
- Ball joint attachment areas and other stress points on the arm are additionally reinforced for heavy conditions;
- Arm bushing protectors are produced of Japanese Chloroprene Rubber, the best material guaranteeing long service life.
Quality management system of Masuma bars is ISO / TS 16949 certified (special requirements for ISO 9001: 2008). Corporate standards are used for the assessment of suppliers for vehicle manufacturers (for example, ASES - the standard of the Renault-Nissan concern).
The plant's own laboratory tests all batches of products using the following methods:
- long-term life tests to assess bar and rod reliability;
- assessment of deformation resistance and impact resistance;
- checking the corrosion resistance of metal;
- testing of silent blocks, ball bearings and other components.
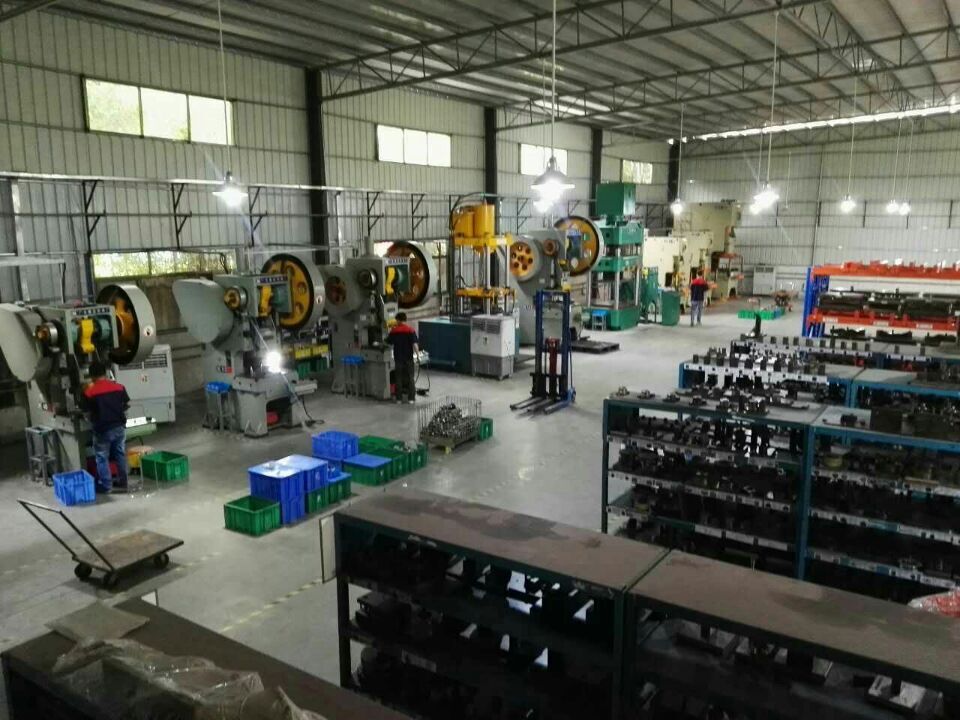
CV JOINT PRODUCTION
Production of Masuma constant velocity joints (CV joints) is carried out according to OEM specifications of vehicle manufacturers and is fully consistent with the manufacturing methods of OEM parts. All metal parts of a CV joint, from body (“tulip”) to inner shafts, undergo mandatory hardening followed by tempering (slow cooling), which gives the metal high strength. Producing of internal CV joint mechanism is fully automated, which guarantees high-precision alignment of moving parts and best tolerances.
During assembly process CV joints are checked with an infrared camera for absence of metal microdefects. When ready, the parts undergo power tests as well as noise and vibration tests.
All Masuma hinges come with a robust boot, clamp and special grease so that you don't have to buy them separately.
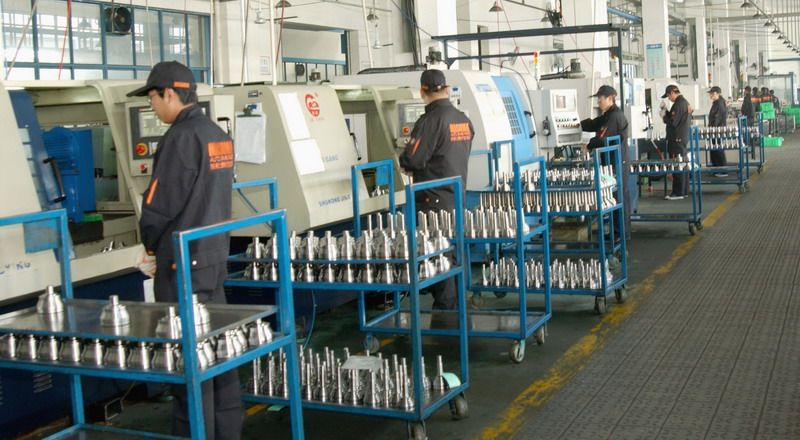
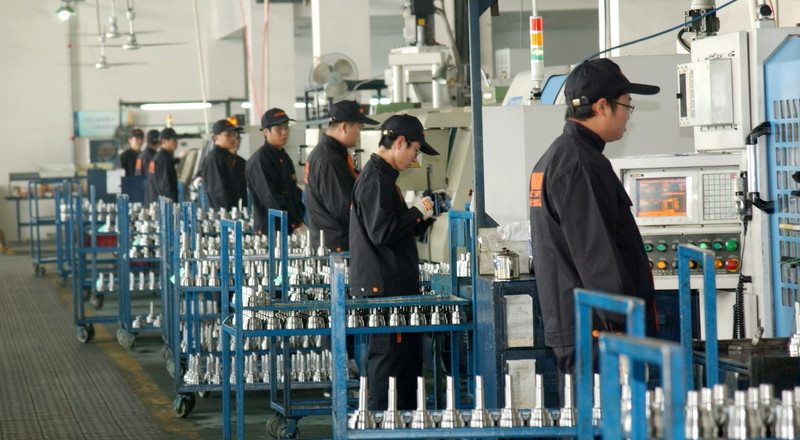
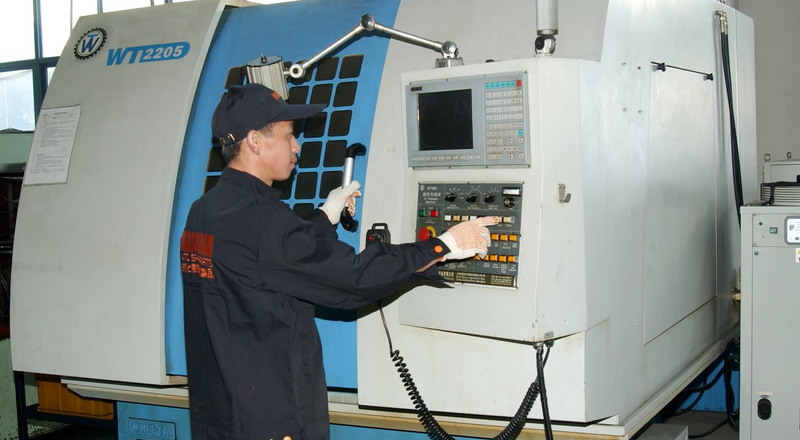